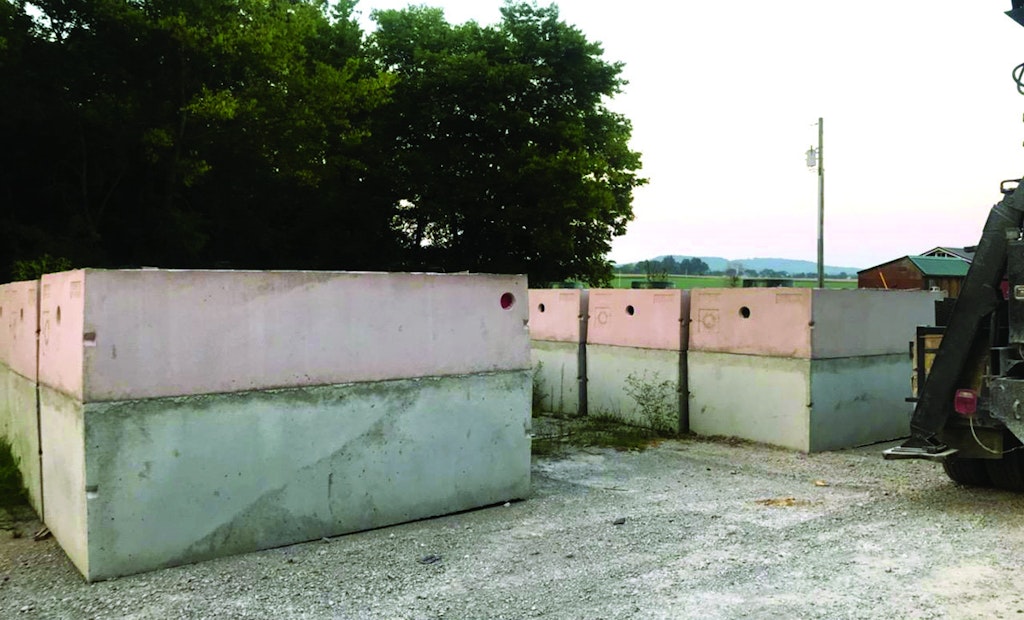
These tanks include an anti-microbial admixture to reduce the likelihood of corrosion caused by hydrogen sulfide gas. (Photo courtesy of David Yoder)
Interested in Onsite Systems?
Get Onsite Systems articles, news and videos right in your inbox! Sign up now.
Onsite Systems + Get AlertsCorrosion of concrete is not a new topic, but it rears its ugly head from time to time. It was first documented and studied in concrete pipes in sewer systems, but it can show up in concrete septic tanks and distribution boxes. The corrosion relies on the presence of unique microorganisms that, when exposed to oxygen and specific gases, secrete acid. This is why it is called microbially induced concrete corrosion. Depending on several variables, this chain of events can take a few years or decades to damage components.
The question arises: Why do some concrete tanks have MICC issues while most do not? Hydrogen sulfide levels in the wastewater increase with the detention time in a septic system and the amount of sulfide varies in water supplies. The damaging biogenic sulfuric acid comes from sulfur-oxidizing bacteria that can form on the concrete surface above the waterline once that surface pH reaches a lower value. The presence of these bacteria depends on the concentration of hydrogen sulfide gas.
The quality of the concrete is an important variable, and a high-quality concrete mix with a low water-to-cement ratio and low permeability is essential to limit the formation and impact of MICC. The decreased permeability improves concrete’s resistance to freezing and thawing, saturation, sulfate, chloride-ion penetration and other chemical attacks. It is essential to reduce the permeability to increase durability, and the water-to-cement ratio should be at most 40% in septic system components.
In addition to the optimal water-to-cement ratio, some products can be added to concrete to reduce the permeability or inhibit the bacteria responsible for MICC.
- Secondary cementitious materials can increase the density and lower concrete permeability. Fly ash, slag and silica fume are just some options. Using one or more of these mineral admixtures in the concrete mix design will increase the strength and density while lowering the porosity and improving chemical resistance. Promising work with nanomaterials also indicates significant permeability reductions with additives like colloidal silica. Colloidal silica-based admixtures used in concrete have reported increased compressive and flexural strengths and reduced water permeability under high hydrostatic pressure. They also change the viscosity of the water, resulting in less bleeding water channels in hardened concrete. Concrete densification can severely slow the rate of pH decrease so that the ideal pH for bacteria colonization is never reached prior to the product’s end of life.
- In aggressive conditions that may lead to MICC, antimicrobial admixtures and sealers can be used, making the concrete uninhabitable for bacteria growth and colonization in septic and pump tanks and distribution boxes. Numerous products on the market could be added to the concrete during manufacturing. They can have some limitations in terms of maximum hydrogen sulfide levels and minimum concrete surface pH, so it’s important to consult with the suppliers on applicability.
ASTM International Committee C13 has developed standards for testing materials exposed to MICC. The committee has approved three new standards in the past few years.
- C1894-22 Standard Guide for Microbially Induced Corrosion of Concrete Products
Overall guide to the phenomenon and guidance on testing.
- C1898-20 Standard Test Methods for Determining the Chemical Resistance of Concrete Products to Acid Attack
Concrete test procedure for strong acid exposure (later stages of MICC).
- C1904-22 Standard Test Methods for Determination of the Effects of Biogenic Acidification on Concrete Antimicrobial Additives and/or Concrete Products
Test procedures for additives or concrete products to assess performance during the bacterial attachment phase (Stage 2) of MICC.
If you are considering a concrete additive or sealer, determine if they have been tested to the following standards:
- ASTM C1904, Test Method A: Standard Test Methods for Determination of the Effects of Biogenic Acidification on Concrete Antimicrobial Additives and/or Concrete Products.
- ASTM D4783: Adapted for determination of antibacterial resistance of concrete to Thiobacillus species. Reduction of bacterial growth in 24 hours.
GO TO THE SOURCE
There are considerations when you have existing tanks showing impacts from MICC. Recently, the National Precast Concrete Association has been performing research to better understand the unique conditions in septic or pump tanks where corrosion is found. There is convincing evidence that much of the hydrogen sulfide gas feeding the bacteria comes in from the top of the outlet tee.
A potential explanation for that is that the hydrogen sulfide gas remains trapped below the waterline due to calm conditions and the existence of a scum layer. Then, when it flows through the effluent filter and out, there is a sudden increase in turbulence and water-air interface. This results in a dramatic release of hydrogen sulfide gas, which can then escape up and back into the tank via the open effluent tee.
Other possible explanations include the gas coming from turbulence downstream in an equalization tank, pump tank or distribution/dropbox or directly from the soil area.
For MICC to occur, turbulence is the most common process that releases hydrogen sulfide gas into the airspace. Septic tanks are designed to minimize turbulence, but some tanks can experience turbulence, increasing hydrogen sulfide release. Examples of such tanks include where wastewater is pumped into the tanks from grinder or ejector pumps, high peak flows or pump tanks with turbulence.
Steps should be taken to reduce the turbulence in these tanks. When effluent is pumped from the structure into the septic tank, it is best to pump it into the sewer line as far from the septic tank as possible on low volumes with a small pump. In the pump tank, a tee can be extended to near the bottom of the tank to minimize splashing.
Every material has a mechanism by which it can be damaged. Having the knowledge and understanding of MICC is helpful, along with the potential solutions available to protect concrete and reduce the risk of MICC.